Aktualności / Pięć twarzy KROE
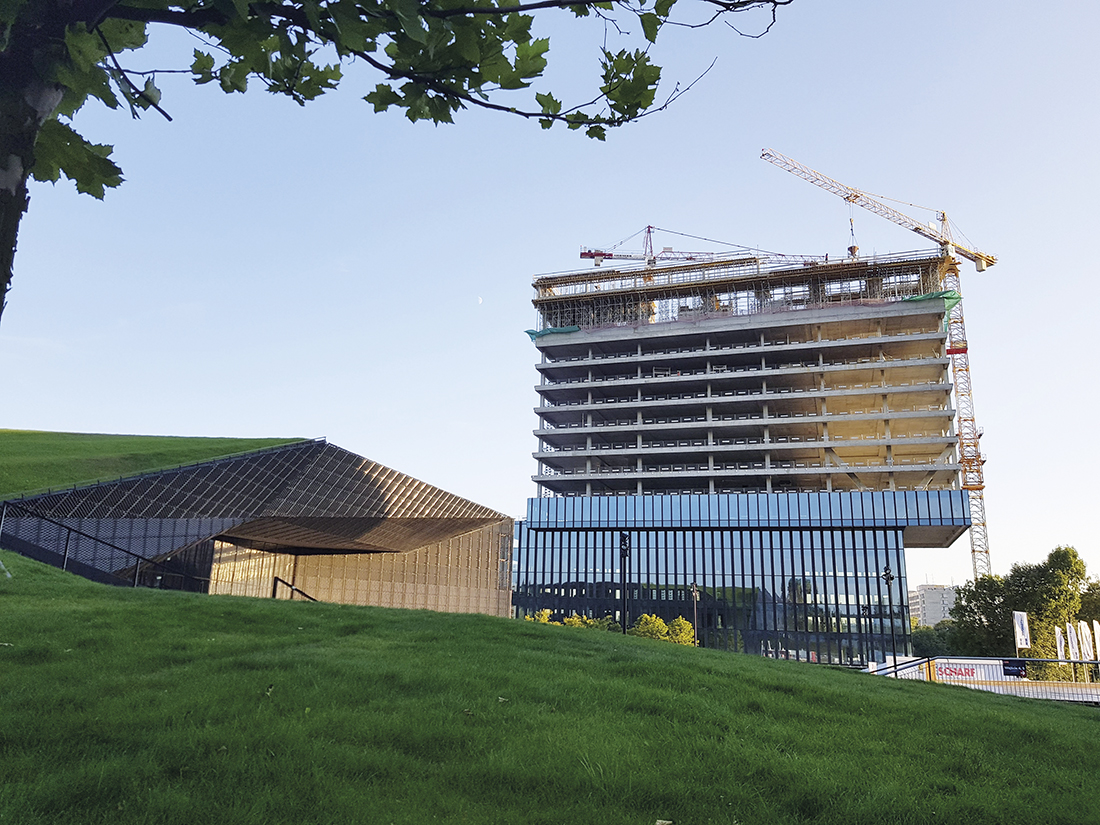
Zuchwałe geometrycznie okładziny wiszą na portalach domu akademickiego w dzielnicy Croydon w Londynie. Na dwóch wieżowcach KTW w Katowicach zawieszono wertykalne żyletki, czarne jak węgiel. W biurowcach Podium w Krakowie cementowe płyty dekorują wnętrza. Dom pani Alicji w Warszawie jest betonowy do granic; elewacje, ogrodzenie, nawet skrzynka na listy i kominek w salonie zostały przykryte okładzinami. W restauracji hotelu Stary w Krakowie goście siedzą pod cementowymi lampami. Wszystkie realizacje wyszły spod ręki KROE, która w Skawinie pod Krakowem zajmuje się produkcją prefabrykatów GRC.
Węgiel na szkle
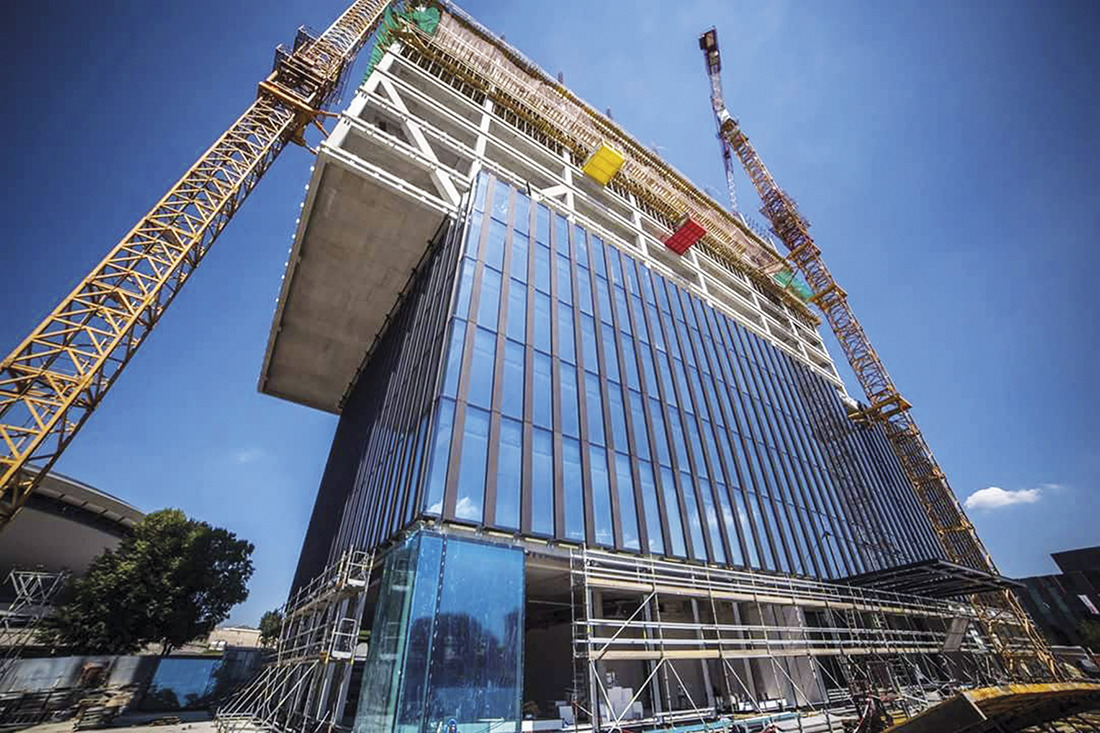
Wycieczkę po realizacjach KROE można rozpocząć od Katowic. Wieżowce KTW są projektowane przez słynną śląską pracownię Medusa Group. Stanęły w Strefie Kultury przy rondzie Ziętka. Za sąsiadów mają Spodek, Międzynarodowe Centrum Kongresowe, nową siedzibę NOSPR-u i nowe Muzeum Śląskie. Obecnie nie ma w Katowicach bardziej rozpoznawalnego adresu. Budowa KTW 1 (wysokiego na 66 m) zakończyła się w 2018 r., budowa KTW 2 (134 m) jeszcze trwa. Niższy składa się z dwóch prostopadłościanów stojących jeden na drugim, ale przesuniętych względem siebie. Wyższy został podzielony na trzy podobne bryły. Fasady biurowców są zbudowane ze szklanych paneli na aluminiowej konstrukcji, do których przytwierdzono cienkościenne prefabrykaty GRC. Charakter prefabrykatów, ich rolę na elewacji, optyczny ciężar, estetykę, fakturę i kolor ustalają architekci. Dynamika i dyscyplina oszczędnej formy to znaki firmowe projektów wychodzących z pracowni Łukasika i Zagały. W KTW wizualnie bardzo lekkie pasy antracytowego betonu pną się z dołu do góry przez wszystkie kondygnacje. Na obu budynkach prefabrykaty są bardzo wysokie i wąskie. Betonowe żyletki mają najczęściej 3,65 m wysokości (pełna kondygnacja), ale szerokość elementów się zmienia. Na najniższych kostkach obu wieżowców płyty mają 59 cm, na wyższych zwężają się do 39 cm. Zwieńczeniem KTW 2 jest podwójnej wysokości trzecia kostka i na niej prefabrykaty mają jedynie 19 cm. Przy takich rozmiarach problemem może być utrzymanie sztywności elementów, bo płyty są grube tylko na 4 cm.
Jak być sztywnym

Podstawowym gwarantem trwałości prefabrykatów produkowanych przez KROE, niezależnie od charakteru zamówienia, jest technologia spray, stosowana przy ich wytwarzaniu. Z Katowic przenosimy się na halę produkcyjną pod Kraków. Spray polega na natryskiwaniu na matrycę mieszanki betonowej i równoczesnym dozowaniu ciętego włókna z podajnika. Włókno cyrkonowe, pełniące funkcję zbrojenia, nie jest wcześniej mieszane z betonem. Połączenie betonu i włókna następuje w ostatniej chwili, w strudze mieszanki, a potem w wyniku ręcznego wałkowania kolejnych natryskiwanych warstw. Dzięki temu włókno układa się w betonie tylko w jednej, pożądanej płaszczyźnie (2D), a wytrzymałość takiego elementu na zginanie jest nawet trzykrotnie większa niż w technologii zalewanej. W utrzymaniu sztywności płyt elewacyjnych KTW pomaga też głęboko fakturowany front prefabrykatów. Zaproponowany przez architektów ryflowany wzór kształtem przypomina blachę trapezową. Poza tym przy długich i wąskich elementach wyzwaniem staje się skurcz betonu. Wąski element o długości 4100 mm, a tyle mierzyły najwyższe płyty, może się skurczyć do ok. 4050 mm (0,1 proc.). Technolodzy KROE musieli uwzględnić to zjawisko. Realizacja płyt na drugi wieżowiec jest na ukończeniu, ostatnia partia powinna opuścić zakład w Skawinie do końca roku. W sumie na obu budynkach znajdzie się ponad 9 tys. m2 czarnych cienkościennych elementów.
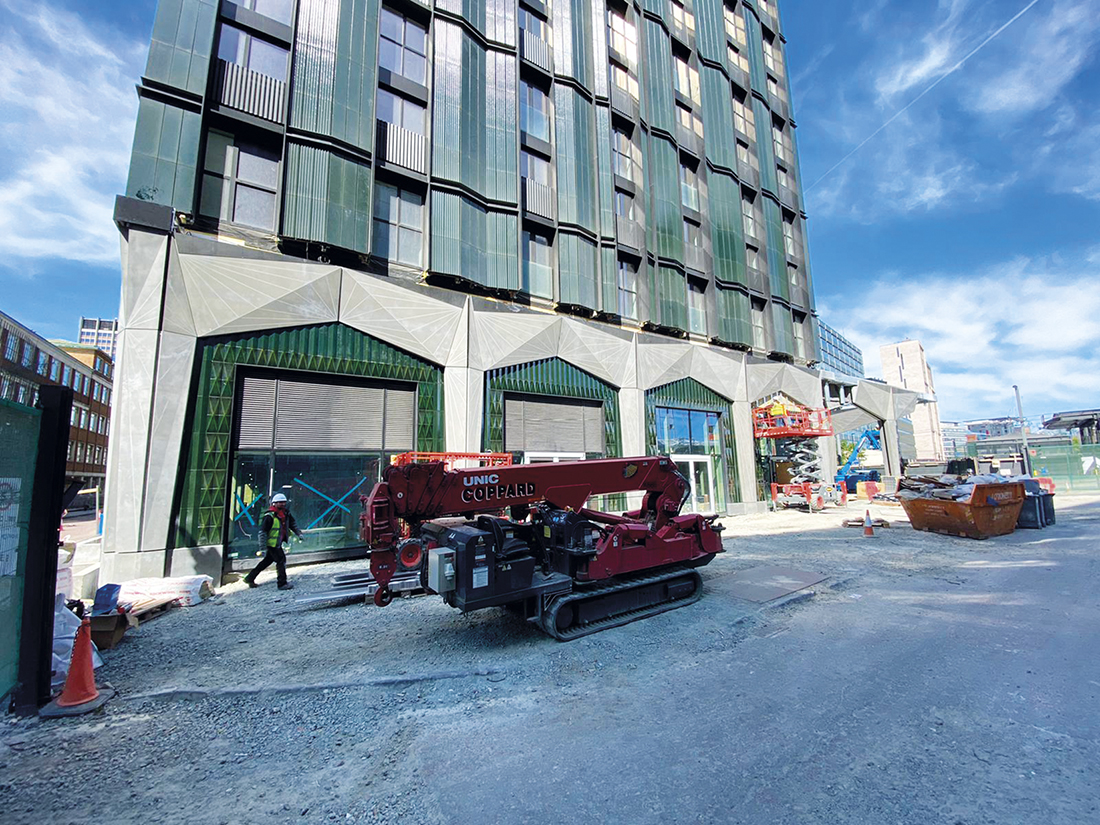
Anglicy na bogato
Patrząc na szaloną fasadę budynku w londyńskim Croydon, trudno się domyślić, że stoimy przed zwykłym akademikiem. Z zewnątrz wydaje się prawdziwie luksusowy. Od pierwszego piętra w górę został obłożony malachitową ceramiczną okładziną. Natomiast cały wysoki parter budynku należy do KROE. Ilościowo zamówienie nie było duże, około 900 m2, czyli dziesięć razy mniej niż w Katowicach. Jednak dla firmy było to pierwsze tak skomplikowane zlecenie, w dodatku na wymagającym rynku brytyjskim, gdzie technologia GRC się narodziła. W tym mieście sukces bądź porażka mogą wiele znaczyć. Na fasadzie budynku w Croydon prefabrykaty zasadniczo się nie powtarzają. Nawet jeżeli geometria niektórych elementów jest bardzo podobna, nieznacznie zmieniają się ich wymiary. Nawet jeżeli wymiary płyt różnią się między sobą tylko o kilka centymetrów, oznacza to, że dla każdego elementu należy przygotować osobną formę. Geometria płyt była karkołomna. Formy na beton, które w linii prostej miały 3-4 m długości, były składane z trójkątnych szalunków, łączonych ze sobą pod różnymi kątami. Ze sklejki powstały łamane formy-negatywy, podobne do pełnowymiarowych przestrzennych rzeźb. Przygotowanie szczelnych form było możliwe, bo w stolarni KROE pracują ludzie z 25-letnim doświadczeniem. Są obeznani ze stolarstwem meblowym, czują materiał pod palcami i intuicyjnie znają jego możliwości. Formy były natryskiwane szarą mieszanką, a po rozformowaniu, miesięcznym sezonowaniu i impregnacji, zostały poddane dalszej obróbce. Z pobieżnego przeglądu realizacji GRC na Wyspach można odnieść wrażenie, że Brytyjczycy gustują w spektakularnych rozwiązaniach. Portale w Croydon to wrota do współczesnego pałacu. Życzeniem zamawiającego było, aby w składzie betonu znalazła się mika, dająca efekt delikatnego migotania elewacji. Mika, teraz nieco zapomniana, przed wojną była stosowana w Polsce w tzw. szlachetnych tynkach na eleganckich modernistycznych kamienicach. Na życzenie inwestora prefabrykaty były piaskowane (Anglicy lubią efekt odsłoniętego kruszywa), a w niektórych miejscach dodatkowo malowane. Nie lada wyzwaniem był transport na budowę wrażliwych płaskorzeźb. Ze względów bezpieczeństwa w drodze do Londynu nie robiono przeładunków. Na ciężarówce jechało maksymalnie sześć elementów ułożonych w trzech paletach, po dwa prefabrykaty, jeden na drugim. Każda paleta ważyła ok. 1,5 tony.
Pustki przed oczami
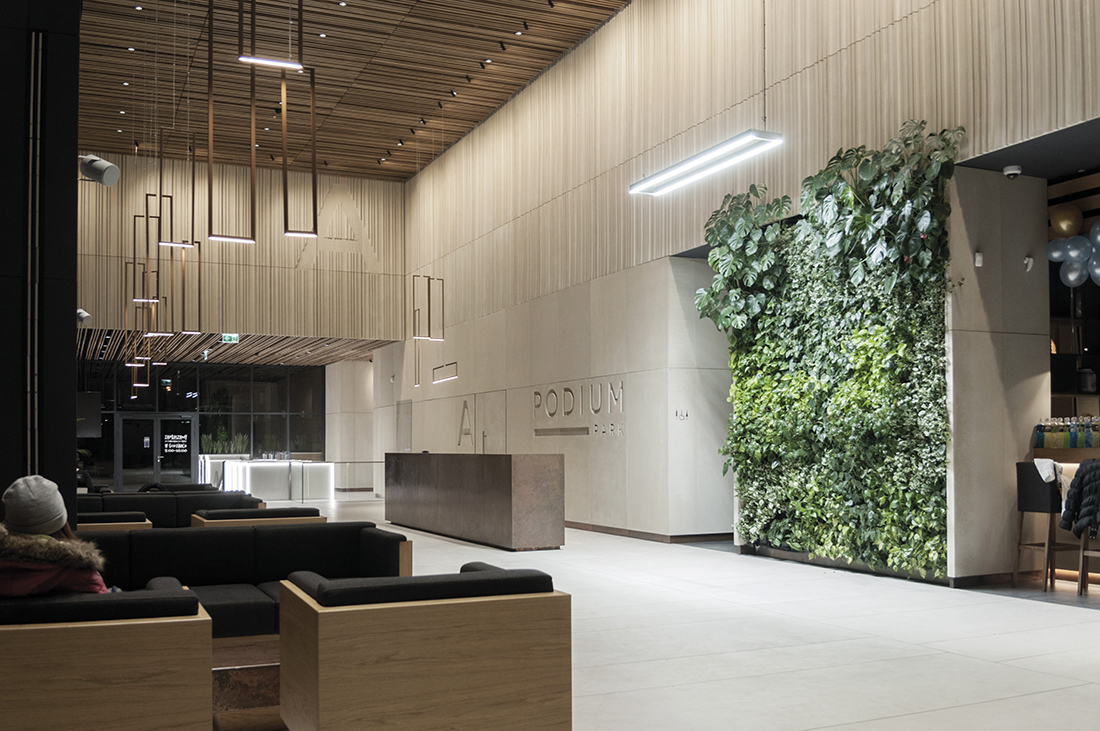
Wypatrywanie cementowych fasad na budynkach Podium Park nie ma sensu. W tej inwestycji prefabrykaty schowały się do wnętrza. Dotychczas powstały dwa z trzech planowanych biurowców przy al. Jana Pawła II w krakowskich Czyżynach. Budynki projektowała pracownia URBA Architects. KROE wykonało płyty do holi głównych na parterze i holi windowych na dziesięciu piętrach. Jest różnica w percepcji prefabrykatów w zależności od tego, w której strefie budynku się znajdują. Na okładziny elewacyjne przeważnie patrzy się z dołu lub z pewnego dystansu, rzadziej z odległości metra czy dwóch. Fasady działają raczej tektoniką, ciężarem, rysunkiem, słowem – całością wrażenia. Będąc we wnętrzu, łatwiej uchwycić detal. Mimo to produkcja płyt elewacyjnych i płyt wnętrzarskich prawie niczym się nie różni. Dokładność procesu technologicznego jest podobna. W tym miejscu dochodzimy do paradoksu betonu i płyt GRC. Życzeniem inwestora było, aby „beton przypominał beton”, czyli na licu płyt były wyraźnie widoczne pustki powietrzne. Pustki na powierzchni betonu architektonicznego oficjalnie są uważane za błąd technologiczny, którego należy unikać. Mogą świadczyć o braku staranności wykonawcy. Jednocześnie te same pustki są specyficzną cechą, która wizualnie odróżnia beton od innych materiałów budowlanych. Można powiedzieć, że laik kojarzy beton przede wszystkim z niejednolitą fakturą i w zależności od poglądów uznaje to za błąd nie do przyjęcia, albo przeciwnie, za niepowtarzalne zjawisko i zaletę architektury. Technologia spray, stosowana w KROE przy produkcji GRC, jest tak dokładna, że eliminuje ryzyko powstania pustek powietrznych na licu prefabrykatu. Lico płyty jest gładkie, inaczej mówiąc – prawidłowe i w pełni zgodne ze sztuką. Co w sytuacji, gdy klient domaga się betonu z „udawanymi błędami”? W tym wypadku technologia produkcji się nie zmienia, jedynie w czasie przygotowania matryc należy użyć drobnego fortelu. W pierwszym kroku na płaskim szalunku wylewa się dość gęstą mieszankę, która nie do końca zagęści się prawidłowo. Po rozszalowaniu na powierzchni betonu ukazują się pustki, małe wgłębienia rozmieszczone w przypadkowym układzie. W dalszej kolejności powierzchnię płyty pokrywa się półpłynną żywicą, z której powstanie docelowa matryca. Stwardniała matryca jest odrywana od płyty. Na jej powierzchni dokładnie odwzorowuje się (jako negatyw) faktura betonu z drobnymi wypustkami. Elastyczna matryca jest teraz podstawą do seryjnej produkcji właściwych prefabrykatów. Na nią natryskuje się mieszankę betonową w technologii spray. Powstają płyty zgodne ze sztuką, które zachowują wszystkie zalety i przewagi wynikające z technologii natryskowej. Jednocześnie sprawiają wrażenie naturalnego monolitycznego betonu, który na co dzień nie jest wolny od drobnych wad. Dla biurowca Podium B powstało kilkanaście elastycznych matryc, każda z innym układem pustek, aby podobna faktura nie powtarzała się na sąsiadujących ze sobą prefabrykatach.
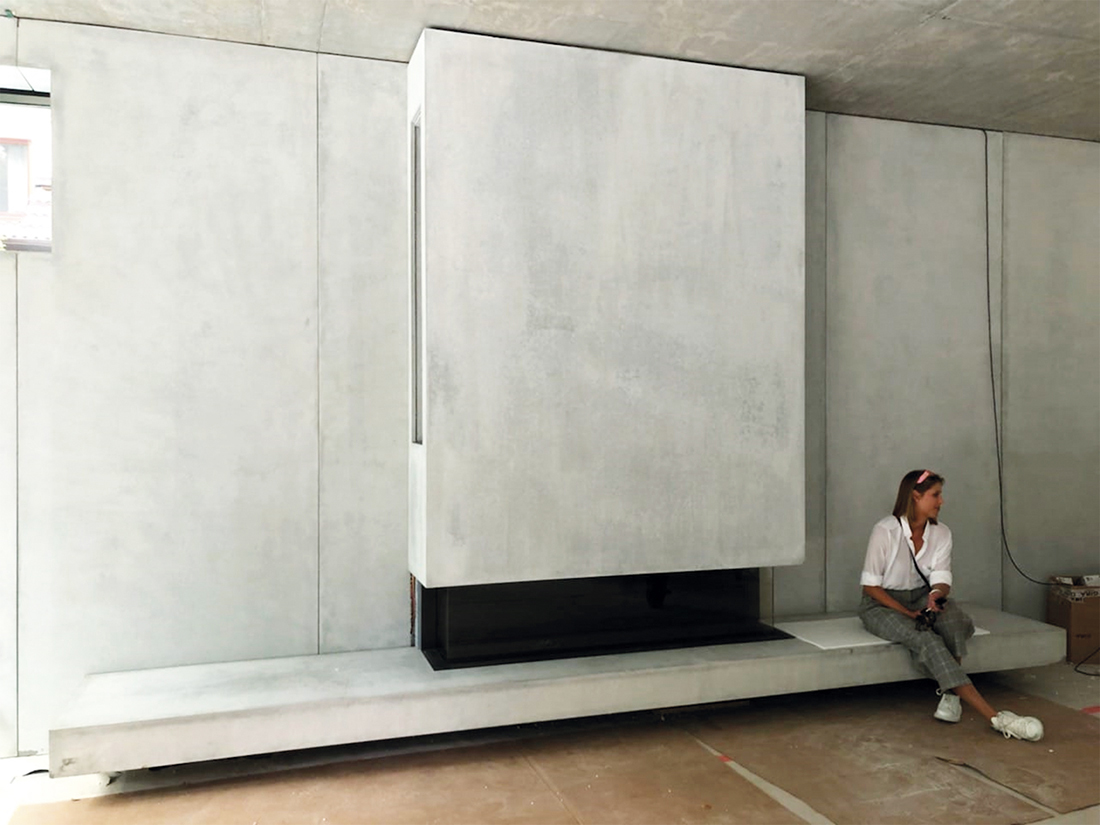
Pani Alicja w krainie płyt
Prywatne zamówienia mają niepowtarzalny koloryt. Stoją za nimi ludzie znani z nazwiska, a nie korporacyjne działy dużych firm. W architekturze domu da się wypatrzeć marzenia, smak i temperament właściciela. Nie wszyscy wiedzą, czego konkretnie oczekują od projektantów, ale niektórzy wiedzą aż za dobrze. KROE przygotowało prefabrykaty GRC dla kilku prywatnych domów. Najbardziej efektowny jest z pewnością dom pani Alicji, znajdujący się w Warszawie i w lesie jednocześnie. Tak właśnie położonych i przez to niezmierne atrakcyjnych działek w stolicy nie brakuje. Konstrukcja domu powstała z betonu i pustaków ceramicznych, za to prawdziwie spektakularne są elewacje. Coraz częściej zdarza się, że w prywatnej rezydencji właściciel zamawia pięć-sześć prefabrykatów na fasadę lub jako wystrój fragmentu ściany w kuchni, pokoju czy łazience. Fragmentu – a nie całości i tylko jako dodatek – a nie jako treść. Posiadanie w domu jakiegoś betonowego detalu, nieprzesadnych rozmiarów, zaczyna być nawet modne. Panią Alicję nie interesował beton robiony na sztuki, dlatego wybrała rozwiązanie ekstremalne. Zamówiła okładziny na wszystkie fasady, całe ogrodzenie, bramę, nie wyłączając detali, jak skrzynka na listy. Dla uzmysłowienia sobie skali zamówienia dodajmy, że opiewało na 1000 m2 płyt, czyli jedną trzecią wieżowca KTW 1. Płyty były duże (2,5 m x 3 m; 2,5 m x 4 m), ale nieskomplikowane. Bez dodatkowych faktur, z gładkim licem (bez pustek powietrznych) i w najbardziej naturalnym szarym kolorze. Tym samym w warszawskim lesie zatriumfował brutalizm. A w salonie pani Alicji został zamontowany jeden z największych elementów, jaki kiedykolwiek wyszedł z hali produkcyjnej KROE. Mowa o sięgającej sufitu przestrzennej obudowie kominka, którego dolna lada ma – bagatela – 5,5 m długości.
Wyzwolenie wyobraźni
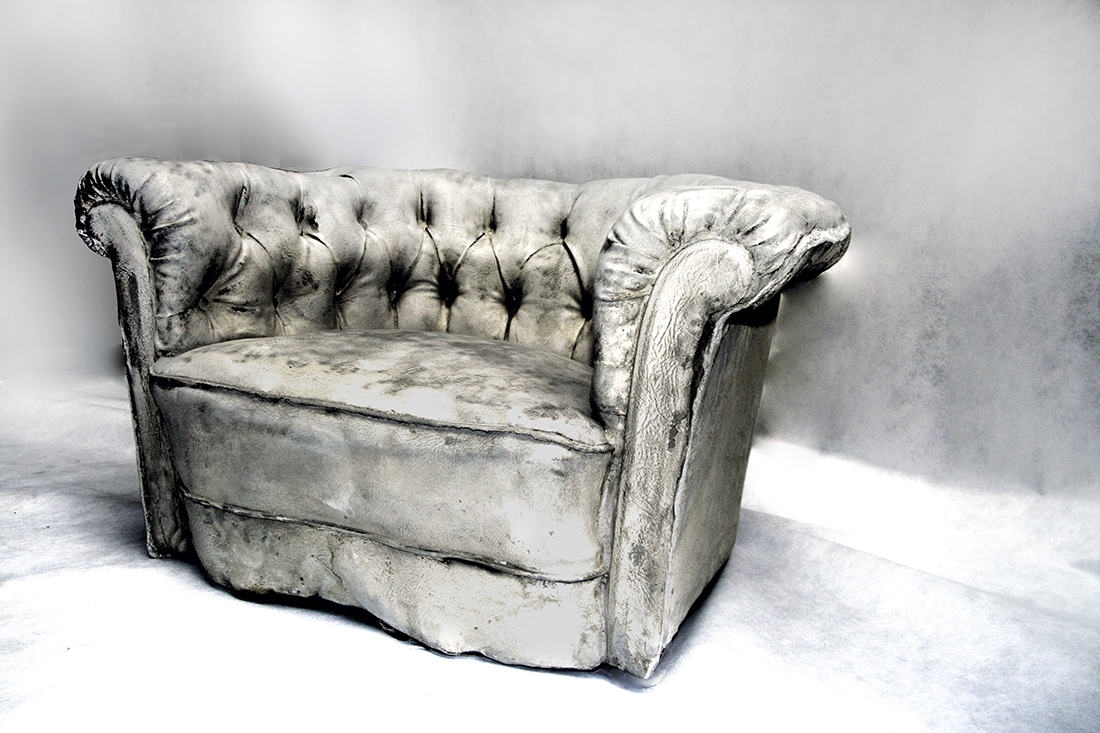
Założyciel KROE Łukasz Żyła mawia, że nie chce słyszeć, że coś jest niemożliwe. W historii firmy duże realizacje zawsze przeplatały się z niepraktycznymi eksperymentami. Nie było w tym specjalnej biznesowej logiki i nie dawało bezpośrednich zysków. Jednak robienie żartobliwych form jest śmiertelnie poważne. Każdy eksperyment poszerza wyobraźnię, podpowiada rozwiązania i otwiera oczy. Jest to odwieczna pogoń za tym, co nieznane. Ktoś powiedział, że zrobienie betonowego odlewu skórzanego fotela Chesterfield jest niemożliwe. Niemożliwe? KROE zaznajomiło się z tematem. Matryca fotela została sporządzona z kilku materiałów różnej twardości od silikonu po żywice. Odwzorowanie formy i faktury mebla było benedyktyńską pracą i trwało trzy miesiące. Skopiowano pikowane obicia, fałdy skóry, guziki i najdrobniejsze detale. Natryskiwanie betonu na formę trwało cały dzień. Fotel był pokazywany w SARP-ie w czasie wręczania nagród Polski Cement w Architekturze. Niestety, z negatywu mogło powstać tylko kilka egzemplarzy odlewu, ponieważ złożona forma szybko ulega destrukcji. Jeden z egzemplarzy ozdabia Wydział Inżynierii Materiałowej i Ceramiki AGH. Fotel pomógł KROE nawiązać kontakt ze światem. Po opublikowaniu zdjęcia w sieci, z firmą zaczęli się kontaktować miłośnicy sztuki z Anglii, Stanów Zjednoczonych, Irlandii i Chin. Z rzeczy bardziej praktycznych, ale nadal wyjątkowych, warto odnotować wystrój restauracji w piwnicy hotelu Stary w Krakowie. Klienci siedzą przy betonowych stołach i pod betonowymi lampami. Lampy nie mogły zbyt dużo ważyć, trudno byłoby się zrelaksować, mając świadomość, że nad głową wisi sto kilogramów. Dlatego metodą prób i błędów udało się osiągnąć złoty środek pomiędzy zachowaniem parametrów materiału a zmniejszaniem jego masy. Klosze lamp powstały jako bardzo cienkie skorupy z mieszanki natryskiwanej na półkoliste matryce. Krótki rekonesans po budowach Krakowa, Katowic, Londynu i Warszawy pokazuje, że GRC ma potencjał. Sprawdza się w dużych komercyjnych realizacjach, w mniejszych projektach wnętrzarskich, wreszcie w całkiem niepraktycznych, ale dających dużo bezinteresownej radości dziełach sztuki.
Paweł Pięciak
Artykuł o nowym budynku Archiwum Narodowego w Krakowie z elewacjami KROE był publikowany w BTA 3/2020
Galeria Zdjęć
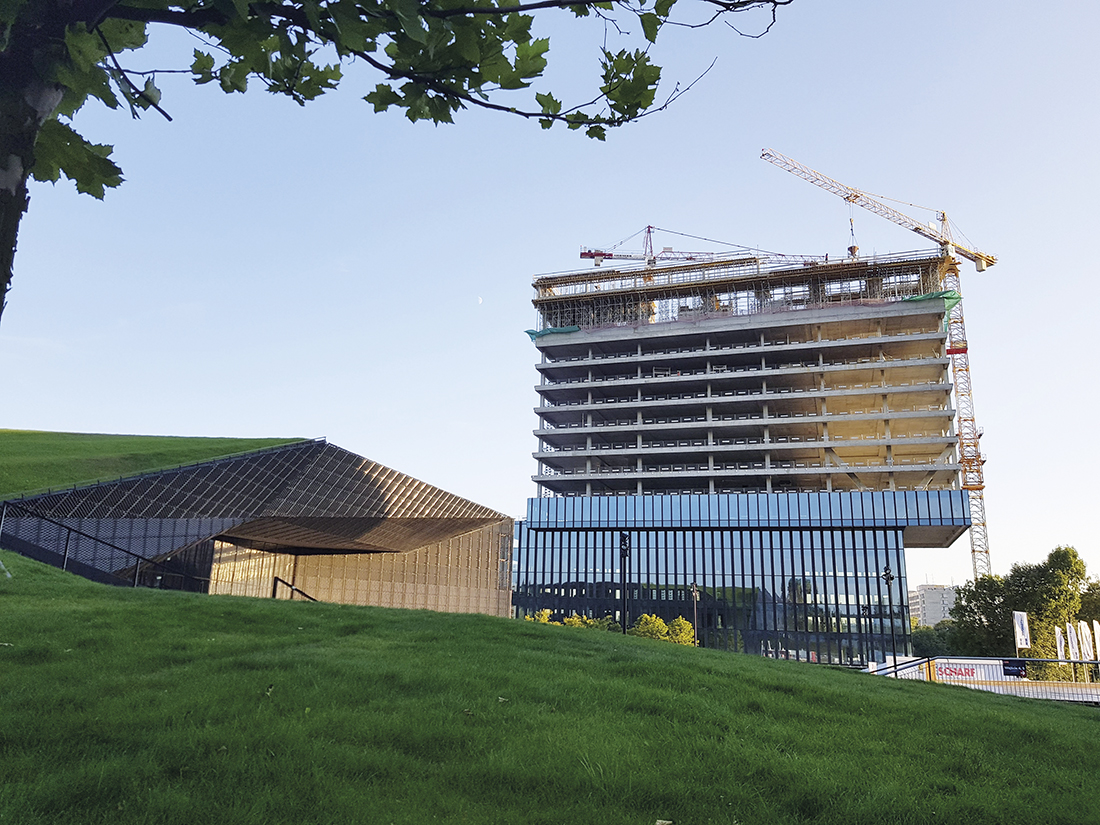
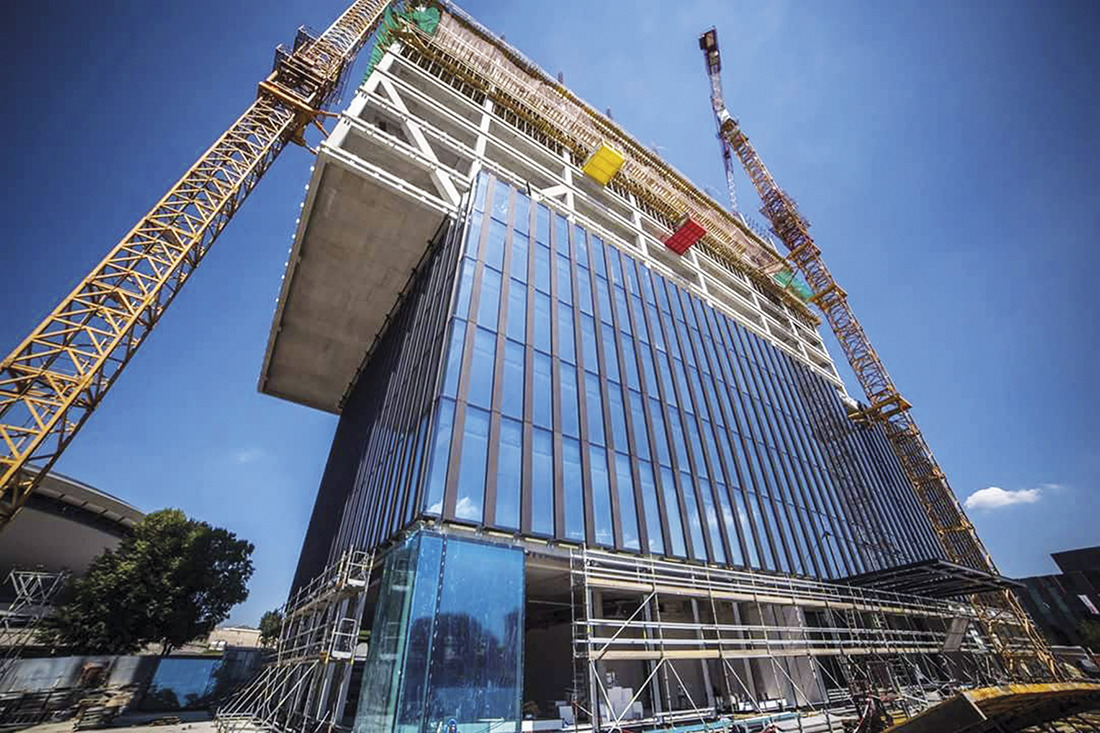

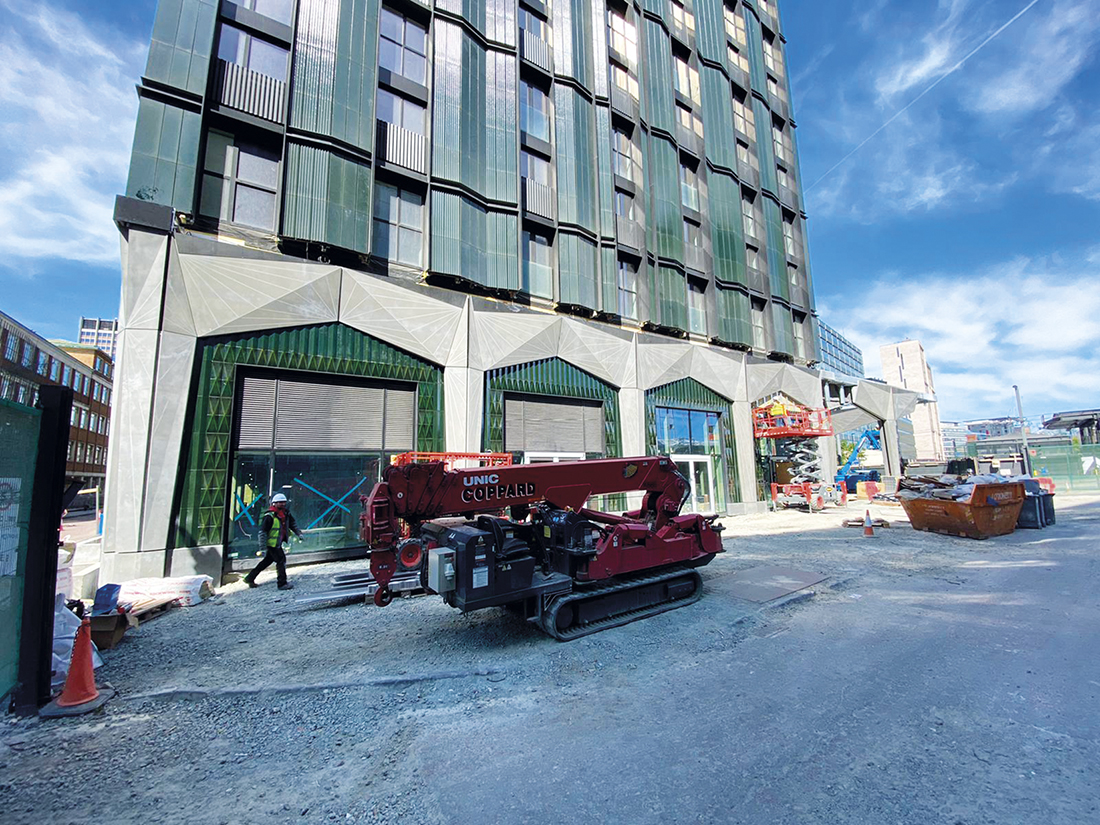
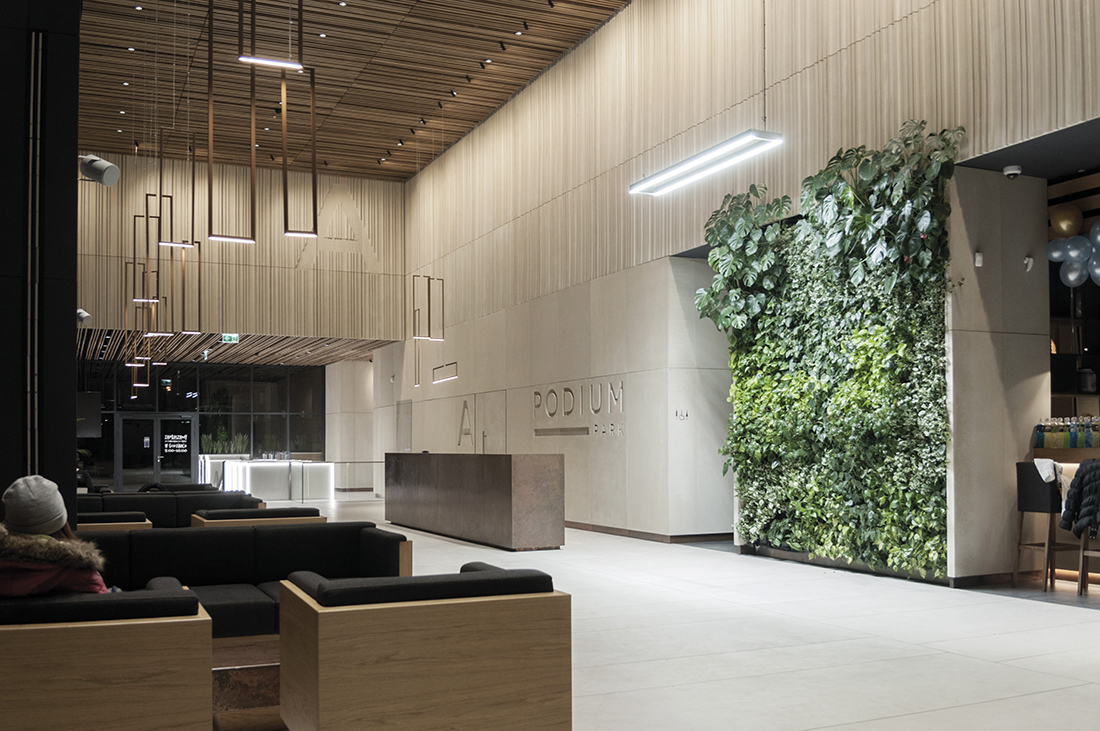
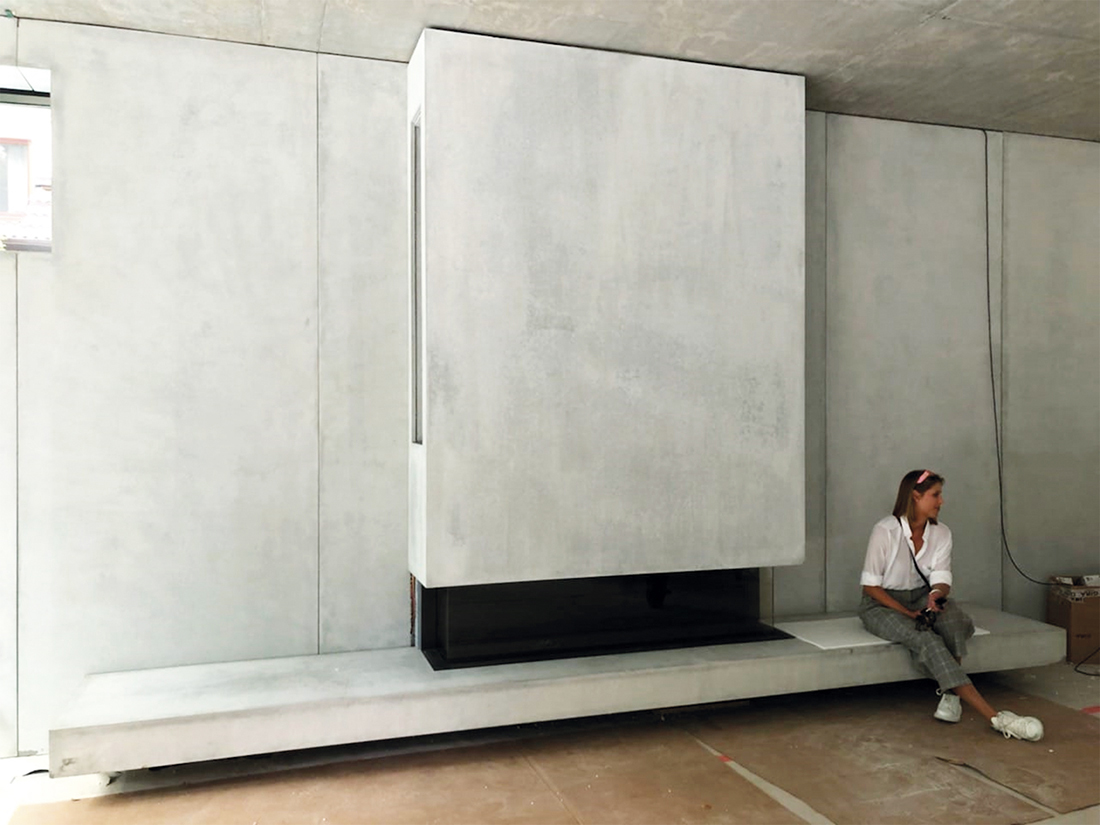
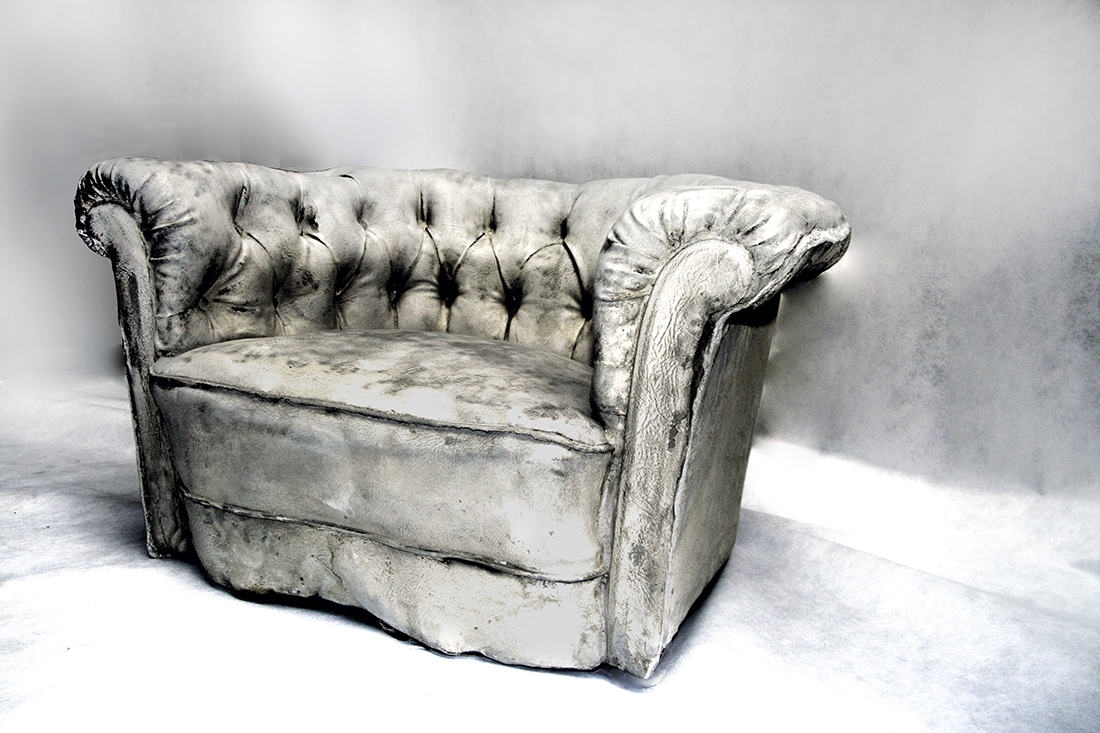
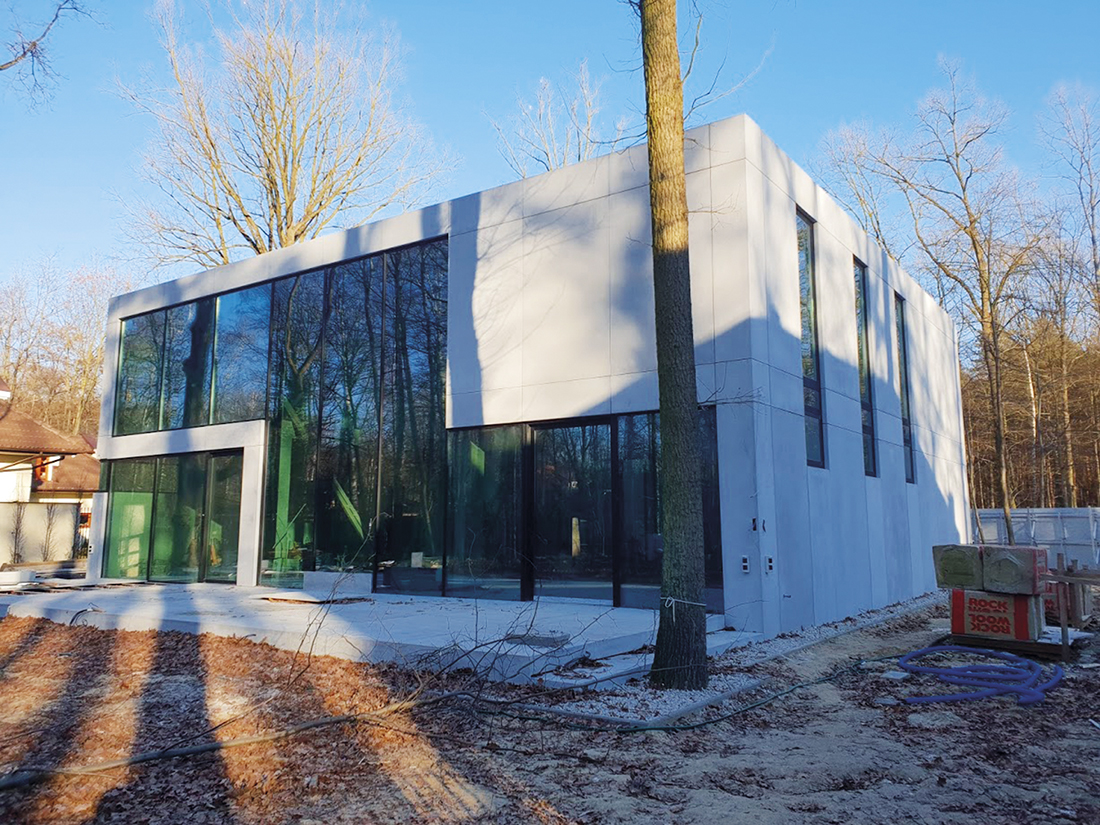
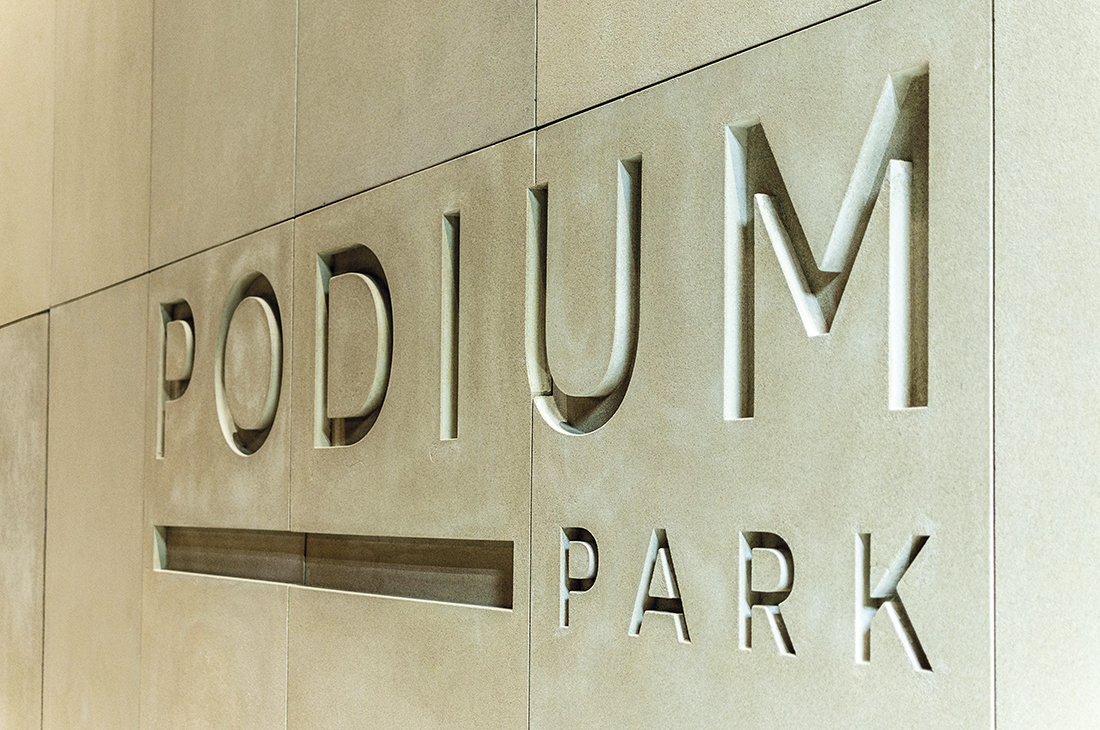